5 min read
How Dirt Makes Dirt: The Hidden Cost of Particulate Contamination
By Jennie Bragg on Wed, Apr. 16, 2025
2 min read
Copper Mine Achieves Amazing Results with Donaldson Hy-Pro
By Hy-Pro Marketing on Tue, Jul. 23, 2024
3 min read
3 min read
Hy-Pro Filtration Helps Paper Mill Achieve 75% Cleaner Oil
By Hy-Pro Marketing on Tue, Dec. 05, 2023
A new case study is available now!
With the help of Hy-Pro Filtration, a U.S. Paper Mill was able to achieve 75% cleaner oil.
1 min read
Updated Hy-Pro App Now Available
By Hy-Pro Marketing on Thu, May. 11, 2023
A new update is available for the Hy-Pro App!
Open this Blog to download below.
2 min read
Factory Side Chat Podcast, Episode 9, Reducing the Total Cost of Ownership with a Kidney Loop or Offline Filtration unit
By Hy-Pro Marketing on Fri, Aug. 26, 2022
Hy-Pro's Factoryside Chat is now available on Apple Podcasts, Spotify, Podbean, and YouTube.
1 min read
Hy-Pro Vac-U-Dry Vacuum Dehydrator (VUD) Explainer Video
By Hy-Pro Marketing on Tue, Jul. 26, 2022
Contamination is Complicated; Removing it is Easy
Check out our latest product explainer video on Hy-Pro's VUD
The optimized balance between heat, vacuum, process design, and an easy, user-friendly operating system for removal of water and particulate from hydraulic and high viscosity lubricating oils. Equipped with generously sized, high-efficiency filtration, the VUD is the ultimate oil purifier. Keeping fluids clean and dry extends component and bearing life, increases productivity, minimizes downtime, and extends useful fluid life. The VUD is ideal for removing all forms of water, including free, emulsified, and dissolved water and gas from hydraulic and lubricating oils.
2 min read
Factory Side Chat Podcast, Episode 8, Partners for Life
By Hy-Pro Marketing on Thu, Jun. 02, 2022
Hy-Pro's Factoryside Chat is now available on Apple Podcasts, Spotify, Podbean, and YouTube.
4 min read
Official Donaldson Hy-Pro Product Catalog for 2025
By Hy-Pro Marketing on Thu, Apr. 21, 2022
The 2025 Donaldson Hy-Pro Product Catalog for Filter Elements and Filtration Equipment is Now Online!
The newest and updated Hy-Pro Filtration Product Catalog is now available online and easier to use than ever before with interactive elements that are not possible in a printed catalog - always available, simple to browse, and information is easy to share.
Click here to view the 2025 Donaldson Hy-Pro Product Catalog
2 min read
Factory Side Chat Podcast Episode 7 Filter Sizing and Selection
By Hy-Pro Marketing on Sat, Jan. 29, 2022
Hy-Pro's Factoryside Chat is now available on Apple Podcasts, Spotify, Podbean, and YouTube.
2 min read
Expanding the distribution of our Podcast; Apple Podcasts, Spotify, and PodBean
By Hy-Pro Marketing on Tue, Oct. 12, 2021
Hy-Pro's Factoryside Chat is now available on Apple Podcasts, Spotify, and Podbean.
8 min read
Precious Metals Mining - Managing the Integrity of Fluids to Reduce Downtime
By Daniel Guerin on Thu, Sep. 09, 2021
Managing the integrity of the fluids used in critical assets to reduce downtime
The risks related to Precious Metals mining can be quite daunting. Commodity price volatilities, Mineral Resources and Reserves estimates, Remote locations, Austere environments, Accidents, Labor, Environmental impacts are just a few of the many inherent risks mining companies must manage successfully.
Intimately tied into these risks are the formidable investment in the assets needed to mine Precious Metals! These assets are exposed to the harsh elements and contaminants found in the mining environment in which they must operate.
3 min read
When New Oil Turns Dark
By Hy-Pro Marketing on Thu, May. 13, 2021
When New Oil Turns Dark
Maintenance professionals who have implemented Oil Analysis Programs (OAP) into their Preventative Maintenance Program understand, at some point, it's going to happen, we don't know when, or where, but one day our new oil is going to start to turn...dark.
4 min read
Four Ways Outside Contaminants Enter Your System
By Scott Howard on Thu, Apr. 15, 2021
Four Ways Outside Contaminants Enter your System
As an equipment owner or manager, the last thing we want to find in our system is contamination. After all, contamination means loss of efficiency or even downtime, which ultimately costs time and money. Contamination somehow always sneaks its way into our systems. So, how does contamination get in our systems and what are we supposed to do about it?
2 min read
The Dollars and Sense of Fluid Cleanliness
By Hy-Pro Marketing on Thu, Apr. 08, 2021
The Dollars and Sense of Fluid Cleanliness
The old phrase will always stand true, "A penny saved is a penny earned." When it comes to businesses and their pennies, every penny counts. When problems during the production and manufacturing process are fixed, people will say "pennies well spent." So, if pennies are so important, then what about dollars? What about thousands, or hundreds of thousands of dollars? What about millions of dollars? In today's production and manufacturing economy, these kinds of numbers are game-changing.
1 min read
Hy-Pro's Product Spotlight: Compact Offline Filter (COF)
By Hy-Pro Marketing on Thu, Apr. 01, 2021
Hy-Pro's Compact Offline Filter
Our newest and smallest unit yet, the Compact Offline Filter is able to fit where no other filtration equipment can. Ideal for smaller systems or where a larger offline system wouldn't fit, this solution can be permanently installed or made portable for ease of use.
3 min read
Getting to Know Demulsibility
By Hy-Pro Marketing on Thu, Mar. 25, 2021
Demulsibility
What is Demulsibility?
Demulsibility is the ability of oil to separate from water. Oil and water naturally separate because like molecules attract each other. Oil sticks with oil, water sticks with water. Oil is "hydrophobic", or "afraid of water," which is a benefit when it comes to fluids like turbine oil.
5 min read
Dynamic Filter Efficiency
By Hy-Pro Marketing on Thu, Mar. 18, 2021
Dynamic Filter Efficiency
What is Dynamic Filter Efficiency?
Dynamic Filter Efficiency matches filter testing with real-life conditions.
All hydraulic and lube systems have a critical contamination tolerance level that is often defined by, but not limited to, the most sensitive system component such as servo valves or high speed journal bearings. Defining the ISO fluid cleanliness code upper limit is a function of component sensitivity, safety, system criticality and ultimately getting the most our of hydraulic and lube assets.
4 min read
Fluid Life Extension
By Hy-Pro Marketing on Thu, Mar. 11, 2021
Extending Fluid Life Saves Money and Helps the Environment
Our mission is to make our customers as efficient as possible, and we achieve that with the highest quality filtration products and total system cleanliness strategies to maximize uptime, productivity and prevent costly fluid contamination related failures. Been there. Done that. Going to do it again tomorrow. But that's not the only way we make our customers efficient. Extending the useful life of in-service fluids pays big dividends in reliability, saves money on premature fluid replacement costs, and reduces the environmental impact of industry by reducing the amount of fluids used and discarded. Enhancing reliability, saving money, and protecting the environment are not only good business, they're our responsibility. To help reduce oil usage, let's first understand why fluids are condemned and prematurely replaced.
1 min read
Bearing and Component Life Extension
By Hy-Pro Marketing on Thu, Mar. 04, 2021
Extending Bearing and Component Life and Saving Money
Improving fluid cleanliness means reduced downtime, more reliable equipment, longer fluid life, and fewer maintenance hours. In addition, it also means reduced component replacement and repair expenses.
2 min read
Understanding ISO Codes
By Hy-Pro Marketing on Thu, Feb. 25, 2021
ISO Cleanliness Codes Explained
The ISO Cleanliness Code (per ISO4406-1999) is used to quantify particulate contamination levels per milliliter of fluid at 3 sizes - 4µ, 6µ, and 14µ. It is expressed in 3 numbers (example 19/17/14) where each number represents a contaminant level code for the correlating particle size. The code includes all particles of the specified size and larger.It is important to note that each time a code increases, the quantity range of particles is doubling. Inversely, as a code decreases by one the contaminant level is cut in half.
1 min read
Removing Water from Diesel; Hy-Pro's Coalescing Technology
By Hy-Pro Marketing on Wed, Mar. 25, 2020
In this Video we provide a brief description and demonstration of Hy-Pro's signature coalescing technology found in our FCLCOD and COT model lines.
4 min read
Steam Turbines and the Battle for Good Demulsibility
By Jennifer Yeadon on Fri, Feb. 01, 2019
Steam turbines are essential to the production of electricity. In fact, over 80% of global electricity is produced by steam turbines.
Demulsibility: Video
By Hy-Pro Marketing on Thu, Jan. 24, 2019
Watch this 5-minute video to learn about Demulsibility and how essential its characteristics are to turbine oil.
4 min read
Industrial Fluid Filtration Best Practices
By Jennifer Yeadon on Thu, Aug. 09, 2018
The world of industrial fluid filtration can get a little...murky. Whether it's a lack of information or just simply not knowing, there are many concepts that may not be clear to someone just entering the industry. That's why we're here -- fluid filtration experts that can guide you through any issue you have. To shed some light and educate, here are some frequently asked questions and their answers.
2 min read
The Benefits of Offline Filtration
By Hy-Pro Marketing on Wed, Apr. 25, 2018
At Hy-Pro, our mission is to make our customers as efficient as possible, and we achieve that with the highest quality filtration products and plans. Our Total System Cleanliness strategies maximize uptime, productivity and prevent costly fluid contamination-related failures. We often achieve that by simply upgrading our customers to Hy-Pro DFE rated filters and Hy-Dry Breathers. But, oftentimes, too many systems have insufficient filtration, or worse off, no filtration at all; this creates the need for a whole range of offline particulate filtration solutions.
6 min read
What to Look for in a Dissolved Metal Analysis
By Jennifer Yeadon on Thu, Mar. 08, 2018
Oil can be high maintenance. It’s not something you just dump in your system and forget about. You have to monitor it, manage it and oversee it. Just letting oil cycle through your system without routinely testing it is a sure ticket to equipment damage.
3 min read
Breathers: An Essential Part of Total System Cleanliness
By Hy-Pro Marketing on Wed, Feb. 21, 2018
Controlling the contaminant flow of your hydraulic, lubricant or fuel reservoirs is one of the simplest goals in achieving Total Systems Cleanliness.
4 min read
Parsing Filter Media and Filter Element Types
By Hy-Pro Marketing on Thu, Feb. 01, 2018
In the fascinating and fundamental field that is industrial fluid filtration, there exist many types of filter elements and many different types of media. In this article, we will briefly cover filter elements and the most common types of media they're made up of. The medias featured below include: cellulose, glass, wire mesh and water removal, coalesce and resin.
3 min read
DFE: Testing Filters Under Real-Life Conditions (Part 4 of 4)
By Hy-Pro Marketing on Tue, Jul. 18, 2017
Throughout the first three entries in this series (find parts one, two and three), we've discussed the difference in two filter element testing methods, ISO16889 and DFE. We've also illustrated how many elements fall short of their stated beta ratio under dynamic flow conditions. Today we'll wrap it up with simulated cold-start tests.
DFE Multi-Pass: Cold Start Contamination Retention
Once the element has captured enough contaminant to reach approximately 90% of the terminal ΔP (dirty filter indicator setting), the main flow goes to zero and the injection system is turned off for a short dwell period. Then the main flow goes to maximum element rated flow accompanied by real-time particle count to measure retention efficiency of the contaminant loaded element. The dynamic duty cycle is repeated to further monitor the retention efficiency of the filter element after a restart.
4 min read
DFE: Testing Filters Under Real-Life Conditions (Part 3 of 4)
By Hy-Pro Marketing on Tue, Jul. 11, 2017
Last week we covered the differences between the ISO16889 Filter Test Procedure and the DFE Filter Test Procedure. This week we illustrate the difference between elements engineered to retain particles during dynamic flow conditions and those that are engineered only to pass the ISO16889 test. (Looking for previous posts? Find parts one, two and four.)
2 min read
DFE: Testing Filters Under Real-Life Conditions (Part 2 of 4)
By Hy-Pro Marketing on Tue, Jun. 27, 2017
Last week, in part one, we briefly discussed how filter elements are rated by manufacturers. This week we're discussing the industry standard ISO16889 multi-pass test and Hy-Pro's standard, the DFE test. (Already read part two? Read parts three and four.)
Current Filter Performance Testing Methods
To understand the need for DFE, it is important to understand how filters are currently tested and validated. Manufacturers use the industry standard ISO16889 multi-pass test to rate filter efficiency and dirt-holding capacity of filter elements under ideal lab conditions.
Figure 1 depicts the test circuit where hydraulic fluid is circulated at a constant flow rate in a closed-loop system with on-line particle counters before and after the test filter. Contaminated fluid is added to the system at a constant rate. Small amounts of fluid are removed before and after the
3 min read
DFE: Testing Filters Under Real-Life Conditions (Part 1 of 4)
By Hy-Pro Marketing on Tue, Jun. 20, 2017
The Dynamic Filtration Efficiency (DFE) Test is Hy-Pro's standard for testing filter elements. Throughout this four-part
First, let's start with the basics.
Why are filters used? How are they rated?
All hydraulic and lube systems have a critical contamination tolerance level that is often defined by -- but not limited to -- the most sensitive system component such as servo valves or high-speed journal bearings. Defining the ISO fluid cleanliness code upper limit is a function of component sensitivity, safety, system criticality and ultimately getting the most out of hydraulic and lube assets.
3 min read
When a Pump Fails, the Whole System Fails: Hydraulic Pump Reliability
By Hy-Pro Marketing on Tue, Feb. 21, 2017
The Problem: Hydraulic Pump Failure
Pumps are the heart of hydraulic systems. When the pump fails, the entire system is down until the pump is operational again. This poses a serious threat to any operation relying on hydraulic systems for productivity.
Recently, a hydraulic valve manufacturer was losing 25 pumps a year on their centralized hydraulic system at a cost of $2,440 each -- and that’s only the pump cost. When you account for maintenance resources, lost oil and lost production, each failure costs ~$25,320.
2 min read
Hydraulic Valve Performance Test Stands and Clean Oil
By Hy-Pro Marketing on Tue, Nov. 29, 2016
The Application
A hydraulic valve manufacturer required pristine fluid (< 14/12/9) to test flow across an 80-micron orifice on their test stand. Gross amounts of contamination in the fluid would skew the test results, invalidating any data collected.
The system held 100 l (26.4
1 min read
Fluid Analysis Reference Guide
By Hy-Pro Marketing on Tue, May. 10, 2016
Do you have trouble translating your fluid analysis reports into useful information you can act upon? If you were to notice high levels of Ba on your report would you know what it is and where its likely coming from?
If you could use a hand we’ve got the perfect tool in our new Fluid Analysis Reference Guide. Within the chart below are contaminants found on fluid analysis test reports listed according to their chemical symbol (often how they'll be listed on the reports) and the various sources from which they are known to occur.
Hopefully, this chart will be a handy reference for reading and analyzing your fluid analysis reports.
1 min read
Filter Sizing: Calculating Clean Element Delta P
By Hy-Pro Marketing on Wed, Nov. 19, 2014
Choosing the best filter element size and media for a specific application can be tricky. You want media that is tight enough to help you reach your target ISO code. However, if you choose a media that is too tight for your application, the element differential pressure (Delta P or ΔP) will rise too quickly and you will be replacing elements far too frequently.
To prevent these situations you should always calculate clean element Delta P whenever changing the filter media or manufacturer.
3 min read
How to Change Out a Filter Element
By Hy-Pro Marketing on Wed, Jun. 11, 2014
Changing a filter element can cause massive contamination ingression if the proper precautions are not taken and the proper procedures followed. We have compiled a step-by-step guide to minimize contamination ingression while changing out elements. Check out how to change out a filter element below
3 min read
[Video] Water Contamination and Removal Methods
By Scott Howard on Mon, Jun. 02, 2014
Do you know what the 3 different types of water contamination are? What about the 4 methods to remove water from your fluid? Watch our short video for a thorough explanation of each.
4 min read
Diesel Fuel Filtration 101
By Hy-Pro Marketing on Wed, Apr. 02, 2014
Reduce unplanned downtime and maximize the fuel efficiency of your diesel engines
Diesel engines are widely used today. You can find them inside buses and tractor trailers traveling our roads, humming along in construction equipment and drill rigs, submerged in marine environments and helping save lives in hospital generators, amongst many other applications. Diesel engines are popular for good reason. Not only do they have cleaner exhaust emissions, they are also known for more reliable starts
4 min read
3 min read
Why You Need to Care About Micro-Dieseling
By Scott Howard on Mon, Jan. 27, 2014
Most people are familiar with diesel engines and how they work, which includes a rapid compression of air. When you inject a fuel source, it creates an explosion. Did you know that micro-dieseling is similar? A front-end loader that runs a diesel engine is a macro-level (or big picture) of what it does on the micro (or smaller) level in a hydraulic pump.
3 min read
Phosphate Ester Acid Remediation
By Scott Howard on Mon, Jan. 20, 2014
1 min read
Unmanaged Phosphate Ester: What Really Happens
By Hy-Pro Marketing on Mon, Nov. 11, 2013
If you deal with phosphate ester (PE) based hydraulic and lubricating fluids, then you likely understand how important it is it to keep it under control. Millions of dollars and thousands of downtime hours are wasted each year by power plants, military and industrial users who need solutions to properly maintain PE fluids. If they're not managed, major damage can take place to your equipment and to your fluids. Let's take a look at what really happens when phosphate ester is out of control.
6 min read
Real Solutions to Bringing Phosphate Ester Under Control
By Scott Howard on Mon, Oct. 14, 2013
If controlling phosphate ester seems about as elusive as lassoing a bucking bronco, then you've come to the right place. Put on your cowboy hat and let's talk about real solutions to getting it under control.
4 min read
What is a Vacuum Dehydrator?
By Scott Howard on Mon, Sep. 30, 2013
If the hydraulic, lubricating, compressor or gear oil you use is not made of a water base in
There are three types of water in a typical system: free water
Using 100ppm for an upper water limit for most systems using mineral base oils, this means all free and emulsified water and a significant portion of dissolved water must be removed.
A vacuum dehydrator is one of the very few methods to remove dissolved water from oil. Let's take a look at these three types of water in your system. It will give you a solid foundation for how the vacuum dehydrator works in the end.
2 min read
Why You Need Proper Filtration in Front of Your Control Valves
By Scott Howard on Mon, Sep. 23, 2013
Proper filtration keeps control valves from becoming faulty and failing.
Most people have at least heard the term control valve, even if they don't know exactly what it does. For those of you caring for hydraulic systems, you likely work intimately with these parts. Did you know that if you're not using proper filtration in front of said control valves that you're likely doing your operation a disservice? (It's true.)
4 min read
[Video] How Big is a Micron?
By Hy-Pro Marketing on Mon, Aug. 26, 2013
If you’ve been following our blog, you probably have a pretty solid understanding of ISO fluid cleanliness codes (if not, click here). You know that ISO codes quantify levels of particulate contamination at three different micron sizes (4μm/6μm/14μm), but how big is a 4μm particle? Watch the video below for a brief explanation of micron size.
1 min read
Eliminating Filter Element Sparking
By Hy-Pro Marketing on Mon, Aug. 12, 2013
Static electricity is an amazing thing. It can cause hairs to stand on end when rubbed with a balloon, which can cause it to then stick to a wall. (It’s a fun trick, especially for kids). Unfortunately, when it comes to interaction with filters, static can have devastating results.
2 min read
Getting Started with Selecting Target ISO Cleanliness Codes
By Hy-Pro Marketing on Mon, Jul. 29, 2013
Here at Hy-Pro, we understand the importance of selecting target ISO Cleanliness Codes. That’s why we’ve put together this set of instructions for selecting target codes in case you’re in need of a little help.
2 min read
How Clean is New Oil? Part 2
By Hy-Pro Marketing on Mon, Apr. 15, 2013
Previously, we discussed how new oil picks up contamination on its way to your facility. Let's take a look at a three more reasons your new oil continues to be contaminated as it reaches your distributor.
2 min read
How Clean is New Oil? Part 1
By Hy-Pro Marketing on Tue, Apr. 09, 2013
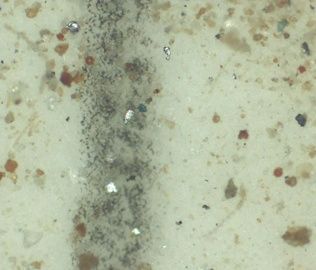
Lubricants and hydraulic oil have to go a long way to make it into your system, which means there's a high potential for it to pick up particulate and water at every step along the way.
Around here at Hy-Pro, we cringe when we think about that process and how our customers put that oil into their machines. We want you to be aware of the state of the oil that you're using, so let's take a look at three reasons why new oil does not mean CLEAN oil.
1 min read
Improving Rolling Mill Lube Oil Performance and Useful Life - Part 3: Solution
By Hy-Pro Marketing on Mon, Mar. 18, 2013
At the end of Part 2, we discussed the winning nature of vacuum dehydration. If you missed Part 1 in the series, you can find it here.
Did you know that hydrogen is the friendliest molecule - meaning that it is most likely seeking partners to attach to? Similarly, the suspended particles in oil actively look for particles to join forces, so they pair with the water.
This particulate contamination is the catalyst guilty of continuing the degradation of the oil and the increase of emulsified water. The more water there is, the more oxidation that occurrs. This also increases various acids that form as the molecules break down. These acids attack seals, hoses, pumps and metal.
2 min read
Improving Rolling Mill Lube Oil Performance and Useful Life - Part 2: Prevention
By Hy-Pro Marketing on Fri, Feb. 22, 2013
If you're just tuning in and didn't catch the first part of our steel mill and lube oil series, click here.
When we left off, we just determined how the high levels of emulsified water and high particulate contamination levels work together to cause bearing failure and reduce oil life. So, how do we prevent this expensive combination from happening? We're glad you asked!
2 min read
Improving Rolling Mill Lube Oil Performance and Useful Life - Part 1: Quality
By Hy-Pro Marketing on Fri, Feb. 15, 2013
Premium oils keep steel mills running. It's crucial to protect their quality in order to keep the mills fully functioning.
In both hot and cold steel mill production, high-demulsibility lubricant is used for backup roller bearing lubrication. Some of these oils are referred to as SD, which stands for super-demulsibility. Not surprisingly, these SD oils are a premium product and come at a premium price. If a manufacturer wants to invest in these big-ticket oils, they obviously want to go to great lengths in order to keep them clean and fully functioning.
Join us for this three-part series as we take an in-depth look at improving rolling mill lube oil performance and useful life.
1 min read
Keeping Clean in a Dirty Environment [Case Study]
By Hy-Pro Marketing on Fri, Feb. 08, 2013
Mining is a dirty business, as you can imagine, and equipment used to aid in mining efforts is not immune to the filth. Yet it is imperative to keep fluid clean. Not only will it save time and money, it lessens the amount of downtime for repairs, which is always a great goal.
5 min read
Hydraulic and Lubrication Filter Types and Locations
By Hy-Pro Marketing on Thu, Jan. 31, 2013
Selecting the right filter can improve the reliability of a system and eliminate failure. With so many options available, we understand how difficult it can be to choose just the right one. Let’s take a look at some of the hydraulic and lubrication filter types and where/how they are predominantly used to help you make the best choice for your filtration needs.
1 min read
How to Prevent Gearbox Failure
By Hy-Pro Marketing on Thu, Jan. 17, 2013
When gearboxes go down, it’s generally because of contamination. This is a costly repair on its own, but once you include the loss of production from downtime, the cost can soar to astronomical figures. Sadly, though, sometimes gearbox failure happens, which wastes your time and money. Let’s take a look at some of the main causes of gearbox contamination and how you can prevent it.
4 min read
[Video] Decoding ISO Fluid Cleanliness Codes
By Hy-Pro Marketing on Thu, Jan. 10, 2013
You likely know that there's a direct link between fluid cleanliness and component life-span. But when it comes to ISO cleanliness codes, does it all look like gibberish to you? If you answered "yes," then we can help. Watch the video below for a great primer on ISO Fluid Cleanliness Codes. You can also find the transcript below the video.
2 min read
Hydraulic Oil Water Removal
By Hy-Pro Marketing on Wed, Nov. 14, 2012
Water, it's a compound that is required for practically everything on the earth. But within a lubrication or hydraulic system, it's one of the most damaging contaminants possible. Unfortunately, it's also one of the most common contaminants you'll find in your system.
When your lubrication or hydraulic system is continuously or even periodically exposed to high water levels, it can result in a mountain of damage. You can find evidence of water contaminant destruction if you look close enough. This damage appears
2 min read
What Are the Causes of Varnish in Hydraulic Oil?
By Hy-Pro Marketing on Wed, Nov. 07, 2012
The Problem of Varnish Contamination
Varnish contamination is the inevitable byproduct of many degradation processes in hydraulic and lubrication systems. The effects of varnish on industrial and manufacturing systems range from the nuisance of minor downtime and routine maintenance to, worst case scenarios, multi-million dollar catastrophic failures of major capital equipment.
8 min read
ISO 4406: What Do Those Numbers Mean in the ISO Cleanliness Codes?
By Hy-Pro Marketing on Mon, Oct. 08, 2012
Guest post today by Dan Helgerson. He is the Technical Editor of the Fluid Power Journal, where this article was originally published.
We have been talking a lot about filtration here at the steel mill. My predecessor had done a remarkable job in educating by example, demonstrating the need for good control of the fluids in our hydraulic and lubrication systems. He had helped stop the leaks and had added well-thought-out filtration systems that have resulted in substantial savings and increased productivity.
There is still a lot of work to be done and in pursuing that we have invited a number of vendors in, each offering an approach to getting and maintaining an acceptable fluid cleanliness level. The one thing that they all have brought to the table is a discussion of the ISO Cleanliness code. I was in a meeting with a group of managers when one vendor began to talk about the code. Being a Certified Fluid Power Accredited Instructor (AI), I immediately saw this as an obvious teaching moment, so I asked, “Does anyone here want to know what those numbers mean?” The answer was a quick and resounding, “No!”
4 min read
Glass or Cellulose Filter Media?
By Hy-Pro Marketing on Mon, Sep. 17, 2012
Glass or Cellulose: Which Hydraulic Filter Media is Best?
There are several distinct differences between glass and cellulose media. Media selection should be based on the required cleanliness and other unique needs of the system. Evaluate the Beta ratio (efficiency), dirt holding capacity, flow versus pressure drop characteristics, etc. A hydraulic filter supplier should be able to supply more detailed test information in addition to what is supplied in the literature.
2 min read
Vacuum Dehydrator VUD: Real-World Results
By Hy-Pro Marketing on Mon, Sep. 10, 2012
Hy-Pro Vacuum Dehydrators Improve Mill Reliability
We Hy-Pro Vacuum Dehydrators already know that maintaining low levels of water in rolling mill lubricating oil can help improve uptime, extend oil life, prevent bearing failures and increase profitability. But, what about an actual example of how a vacuum dehydrator has improved mill reliability?
2 min read
Oil Vacuum Dehydrators: Managing Water in Rolling Mill Lubricating Oil
By Hy-Pro Marketing on Fri, Aug. 31, 2012
In our last post, Improving Rolling Mill Oil with Vacuum Dehydration, we discussed how the
2 min read
Improving Rolling Mill Lubricant Oil with Vacuum Dehydration
By Hy-Pro Marketing on Tue, Aug. 07, 2012
Benefits of Vacuum Dehydration for Rolling Mill Lubricant Oil
Steel mills typically use lubricants with high